Plate fin heat exchangers rank highest among the contestants in the search of ideal thermal control. Essential across many sectors, including aerospace, power generation, and HVAC systems, these heat exchangers are well-known for their great efficiency and small size and design. The features, benefits, and uses of plate fin heat exchangers are discussed in this thorough tutorial together with how best to combine them with screw vacuum pumps to improve their performance.
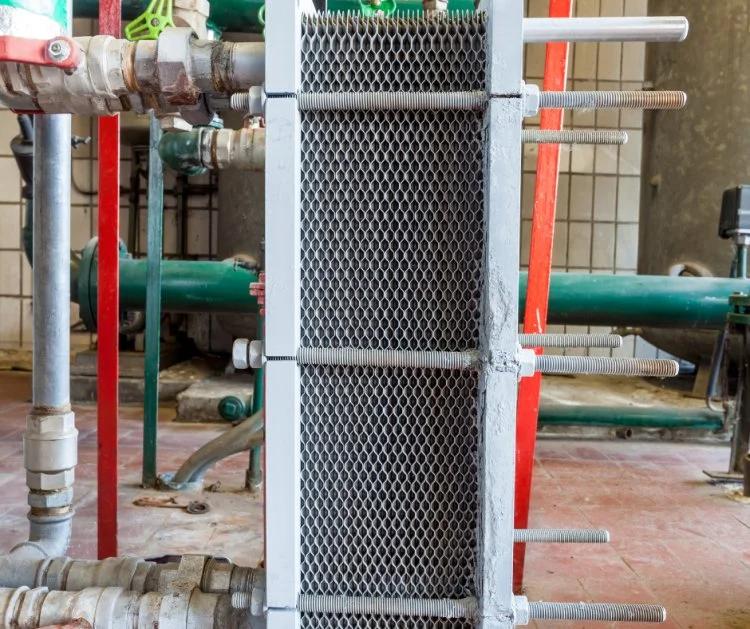
What is a Plate Fin Heat Exchanger
Designed to transfer heat between two fluids utilizing plates and finned surfaces, a plate fin heat exchanger Maintaining a small size, this kind of heat exchanger maximizes the surface area accessible for heat flow. It comprises of several channels through which the fluids might pass by means of a sequence of plates split by fins. Effective heat transfer is guaranteed by the design even in high-temperature and high-pressure surroundings.
How operates a Plate-fin Heat Exchanger?
Plate fin heat exchangers run on the indirectly heat exchange theory. Plates and fins separate the alternating channels the fluids pass through from mingling them away. After the hot fluid heats the plate, it carries the heat to the finned surface. By increasing the surface area in touch with the cool fluid, which absorbs the heat and distributes it, the fins help This mechanism guarantees effective temperature control with lowest possible energy loss.
Advantages of Plate Fin Heat Exchangers
Plate fin heat exchangers provide a few very clear benefits:
- High Efficiency: Excellent heat transfer efficiency resulting from the large surface area the plates and fins offer lowers energy usage.
- Compact Design: Applications with space and weight restrictions would find them perfect since of their compact size and light weight.
- Versatility: Plate fin heat exchangers can handle gas-to–gas, gas-to–liquid, and liquid-to- liquid heat exchange; they are appropriate for a wide spectrum of fluids and operating circumstances.
- Durability: Made of strong materials, these heat exchangers can resist extreme temperatures and pressures, so guaranteeing long-term dependability.
- Low Maintenance: Less frequent maintenance and cleaning needs follow from the design’s minimization of fouling and corrosion.
Applications of Plate Fin Heat Exchangers
Plate fin heat exchangers are fit for a range of uses since of their adaptability and efficiency:
- Aerospace: Designed for environmental control systems and aircraft cooling systems, they guarantee dependability and best performance under difficult situations.
- Power Generation: Crucially important for heat recovery and cooling in power plants, they improve general sustainability and efficiency.
- Automotive: Applied in car cooling systems, they increase engine performance and fuel economy.
- Chemical Processing: Applied for temperature control and heat recovery in many different chemical operations, chemical processing guarantees process safety and efficiency.
- HVAC Systems: Provide effective heating and cooling in homes and businesses to help to save energy and create comfort.
Enhancing Performance with Screw Vacuum Pumps
System performance can be much improved by combining screw vacuum pumps with plate fin heat exchangers. By producing a vacuum atmosphere, screw vacuum pumps reduce the boiling point of the working fluid, therefore improving heat transfer efficiency. Applications needing exact temperature control and the elimination of non-condensable gases—such as those in chemical processing and power generation—will find this mix especially successful. Industries may accomplish exceptional temperature control, energy savings, and process optimization by adopting screw vacuum pumps.
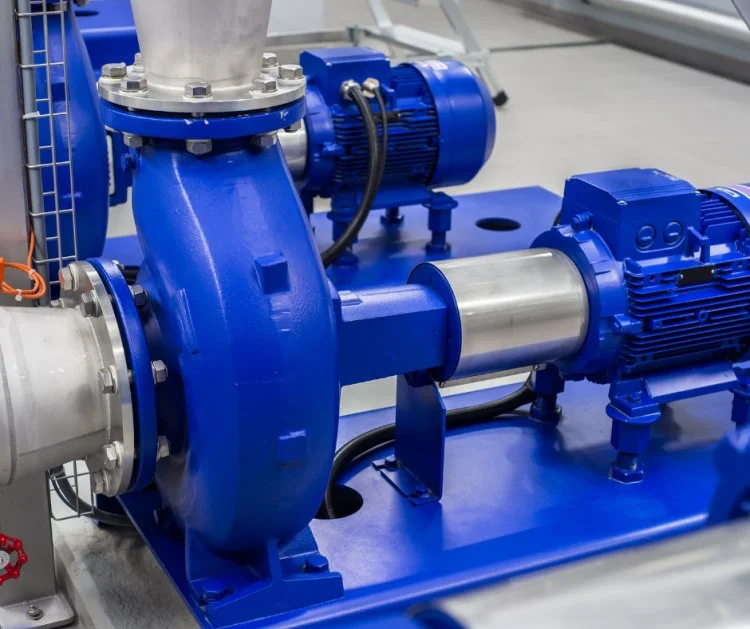
Innovations in Plate Fin Heat Exchanger Technology
Ongoing progress in plate fin heat exchanger technology has produced various developments:
- Advanced Materials: High-performance metals and coatings improve thermal conductivity and corrosion resistance, hence increasing the life of heat exchangers.
- Optimized Designs: Modern designs include improved surface geometries and fin configurations to boost heat transfer area and hence efficiency.
- Compact Configurations: Advances in manufacturing processes have produced more lightweight and compact heat exchangers, perfect for uses with space and weight restrictions.
- Smart Technology Integration: Including sensors and IoT features lets one monitor heat exchanger performance in real time and optimize it, therefore guaranteeing optimum efficiency and dependability.
Selecting the Right Plate Fin Heat Exchanger
Selecting the suitable plate fin heat exchanger calls on numerous factors.
- Fluid Properties: The kind and qualities of the relevant fluids define the design and material selection.
- Operating Conditions: As different heat exchangers are made to handle particular ranges, temperature and pressure requirements affect the choosing procedure.
- Space Constraints: Applications with limited space call for small designs.
- Maintenance Requirements: Long-term performance and dependability depend on considering simplicity of maintenance and cleaning.
Conclusion
Leading modern thermal management devices with unparalleled efficiency, small size, and adaptability are plate fin heat exchangers. Knowing their running principles, advantages, and uses will help one choose the correct heat exchanger for certain requirements. Industries can reach outstanding performance and sustainability by including cutting-edge technologies and related systems like screw vacuum pumps. Plate fin heat exchangers remain a pillar of dependable and effective thermal management solutions as developments keep driving the area.
More Stories
Industrial Revolution 4.0 and the Dawn of Industry 5.0
Why Choose Dubai for Your Business? A Guide to Top Business Setup Consultants and Solutions Providers
Durable Custom wax Paper: Keeps Food Fresh